I Make Products
Maximize your manufacturing efficiency!
One of the biggest challenges in modern manufacturing is minimizing downtime, increasing productivity, and reducing costs.
An unexpected breakdown, a poorly planned product change, or limited capacity can disrupt the entire production chain. The Automation Gap Management team helps bridge these challenges, ensuring that your production always operates at optimal efficiency.
With our years of experience in industrial automation, we have solved numerous manufacturing challenges, gaining in-depth knowledge of various production processes.
Based on our experience, the following challenges cause the most headaches for manufacturing companies:

Unexpected Breakdowns and Downtime
One of the biggest risks in manufacturing processes is unexpected equipment failures. A malfunctioning servo drive, faulty sensor, or poorly functioning PLC component can halt production for hours or even days, leading to significant losses.
Our Solutions
Quick Response Time:
Our experts are readily available and can intervene remotely to resolve issues promptly.
Preventive Maintenance Strategies:
Programmed algorithms assist in scheduling periodic inspections and replacements, reducing the likelihood of failures.
Cost Saving:
Even in inactive states, machines can consume significant energy, leading to unnecessary costs and resource wastage. Our standby mode solutions allow non-essential components to be turned off, reducing energy consumption, optimizing operational costs, and extending equipment lifespan.
Automatic Fault Detection and Prediction:
Our standard software and visualizations continuously monitor machine conditions, providing feedback on potential failures.
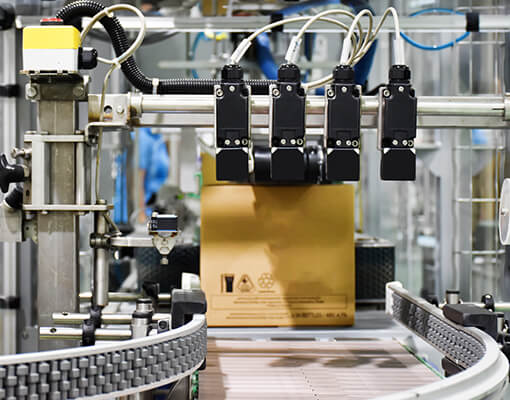
Complicated and Time-Consuming Product Changeovers
Production lines that manufacture various products often suffer from slow changeovers and incorrect settings. A product changeover can take excessive time, and without proper optimization, scrap rates increase, leading to additional costs.
Our Solutions
Automatic Recipe and Parameter Management:
Our PLC control enables the system to automatically switch settings for each product, minimizing unintentional mistake.
Quick Changeovers:
By automating the process, product changeovers become significantly faster.
Quality Assurance:
Our HMI systems provide visual feedback to operators, reducing scrap resulting from incorrect settings.
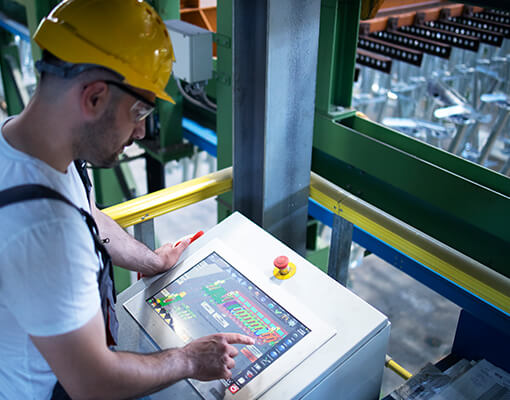
Capacity Issues
– When There’s Not Enough Manpower or Machinery
Continuous production growth often leads to situations where a company lacks sufficient specialists or machinery capacity to handle new projects or increased orders.
Our Solutions
Automation Solutions:
Reduce the need for human intervention.
Efficient PLC Control:
Ensure faster and more precise operations.
Process Optimization:
Achieve higher performance with the same equipment.
Training and Education:
Provide ongoing training to your operators and engineers to keep them up-to-date in system management.
Why Choose Us?

Customized Solutions, Not Template Thinking:
Every manufacturing plant is different; therefore, we don’t offer pre-made solutions. We design automation strategies based on your unique needs.

Quick Response Time and Immediate Availability:
If there’s a problem, you don’t have to wait weeks for a solution. Our team is ready for rapid intervention.

Comprehensive Technological Knowledge and Experience:
We support our partners in areas such as conveyor systems, camera inspection systems, screwdriving stations, heat treatment, soldering technology, leak testing, palletizing, powder coating, and more.

Reliable, Long-Term Collaboration:
We don’t just commission systems; we also provide appropriate training and maintenance support for operators and engineers.

Extensive Product Knowledge:
We have expertise with systems from the leading industrial automation manufacturers, including Siemens, Lenze, SEW, Omron, Mitsubishi, PILZ, Keyence, and many other well-known brands.
How We Work
Safety and Standard Automation:
PLC and HMI programming for safety and standard automation systems.
Backup and recovery:
For PLCs, HMIs, robots, frequency converters, and recipes. Regular backups ensure that in the event of a failure or configuration error, critical settings can be quickly restored, minimizing downtime and losses.
Change Management:
We provide detailed, documented reports for all work we perform, making them fully available to our clients. This ensures complete process transparency, facilitates traceability, and supports more effective decision-making for future improvements.
Operational, Handling, and Maintenance Instructions:
We provide detailed documentation to support operators.
Training and Education:
We offer comprehensive training sessions for your staff.